When choosing a photovoltaic (PV) to their homes, many consumers may ask: how many “plates” do I need? The PV module is popularly known as “plate”, and it consists of a set of cells.
Difference between cell, module and panel
The cell is nothing more than the basic unit designed to perform the direct conversion of solar energy into electricity. The module is a unit formed by a set of electrically interconnected and encapsulated solar cells that generate electricity. And the panels are one or more electrically interconnected photovoltaic modules, assembled to form a single structure. A PV system consists of a set of modules, joined with ancillary equipment (inverters and cables).
Illustration: Carol Rivello
Most information that follows was found at:
RÜTHER, Ricardo. Edifícios solares fotovoltaicos. Florianópolis: LABSOLAR, 2004
Manufacturing of solar module
There are two manners to manufacture a solar module: The first is using solar cells made of extremely thin silicon slices in crystalline form. Usually they are placed between glasses with aluminum frame. This technique is the most traditional and, is currently a larger-scale production on a commercial level.
Did you know?
Silicon is the second most abundant element in the earth’s crust, so there are no restrictions regarding the use of this raw material for the production of solar cells. The limitation here is in getting the silicon with the purity needed to make photovoltaic cells, which requires high technological knowledge.
The second manner is to manufacture modules through plasma application (almost as a “spray”) of a semiconductor material over glass or on other material (which may be flexible) which serves as a “bed”. Afterwards, this assembly is covered with a transparent material, such as glass. The so-called thin film technology is easier to be integrated into urban buildings. The elements used in this case are silicon (in its non-crystalline form, which is called amorphous silicon) or chemical compounds such as cadmium telluride (CdTe) or copper diselenide (gallium) and indium (CIS and CIGS).
Did you know?
This method of manufacture has allowed the development of flexible solar modules, that are unbreakable, lightweight, semitransparent, with curved surfaces that increase the versatility of their application, especially in integration projects of constructions.
In this section you will learn the main existing technologies in the market, which have been sorted according to the raw material from which PV cells are manufactured
Crystalline Silicon (c-Si)
Robustness and reliability have pushed this technology into the photovoltaic market. There are two types of cells: monocrystalline silicon (m-Si) and polycrystalline silicon (p-Si).
- Monocrystalline Silicon (m-Si)
Besides being the oldest PV technology, monocrystalline silicon (m-Si) cells are also the most efficient in commercial applications.
This type of cell is produced by pulling out some sort of seed crystal extremely slowly (at about cm / hour) and uniformly from a molten silicon bath of high purity (Si = 99.99% to 99.9999%) in reactors under controlled atmosphere. This produces a cylinder with two thin ends that are cut out and then the crystal is cut into sections using four slices along its entire length – that will be transformed into squares with rounded corners. Finally, crystal is cut into hundreds of blades (wafers) by wire or diamond saws.
This will be the pre-product used in the production of solar cells, which involves a series of processes such as chemical baths and stoning.
- Polycrystalline Silicon (p-Si)
As the name suggests, these cells are made up of many crystals that are melted and then directionally solidified. It is precisely due to the edges of crystal particles that polycrystalline cells are less effective than monocrystalline cells. Moreover, their production requires less material and energy, resulting in lower final cost compared to monocrystalline.
Hydrogenated amorphous silicon (a-Si)
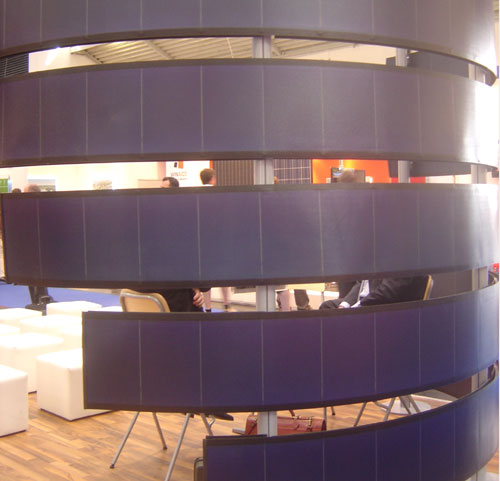
Image: Paula Scheidt
The solar cell of amorphous silicon was the first thin-film technology created. It began to be used in the mid-1970s, soon applied in low-power consumption devices such as calculators, watches and other products with low-power consumption.
The a-Si cells are extremely thin layers of silicon, often no more than 0.5 microns thick with an amorphous structure, which reduces efficiency when compared with crystalline cells. Their efficiency is only 6%, but the cost per square meter is half of crystalline silicon’s. Therefore, if available area is not an issue, technology can be more cost effective.
To manufacture them, a semiconductor is inserted on a substrate (often glass, stainless steel or some plastic) in plasma processing (gas). Then, transparent conductive layers are added to impart electric current. A laser is used to divide the area into several cells, to achieve more appropriate currents and voltages.
Compared to other technologies, it may be more advantageous in warm countries such as Brazil, it presents no decrease in potency with increasing operating temperature.
Cadmium telluride (CdTe)
A thin-film technology as well, a material used initially for calculators to then be sold in modules for large outdoor areas, typically on glass plates. While silicon cells are usually blue or nearly black, CdTe cells are of a brown or dark blue tone.
The low-scale production costs compared to silicon cells are an attractive, and more efficient conversion of solar energy into electrical compared to amorphous silicon (a-Si). The problems related to this technology are the availability of this chemical compound (well below the silicon) and the toxicity of cadmium that, similar to mercury, can accumulate in the food chain.
Copper diselenide (gallium) and e indium (CIS and CIGS)
Solar cells made from the diselenide family of compounds and copper indium (CulnSe2 or simply CIS) and copper diselenide, gallium and indium (Cu (InGa) Se2, or simply CIGS) are quite similar to those of telluride cadmium.
They are not easily manufactured on an industrial scale, reason why companies in this industry took a few years to develop a good production capacity. Due to the aesthetic appearance, these modules are often chosen by consumers to be integrated into buildings, and have good efficiency (amount to 12%, well above the amorphous silicon – a-Si).
However, as CdTe cells, they also present problems relating to toxicity of elements and low abundance.
Colored modules
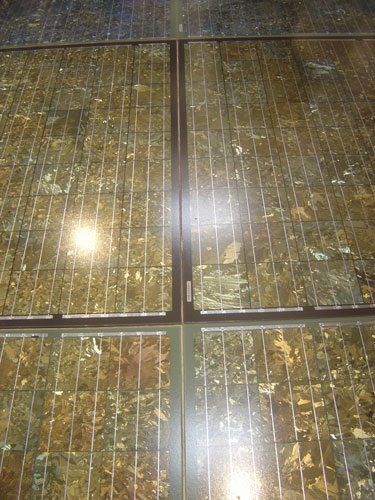
Imagem: Paula Scheidt
Solar panels with crystalline silicon cells are usually blue because this is the color with which the cell has the best efficiency in converting solar energy to electricity. However, there are manufacturers that produce colored panels, such as red or green, in order to attract customers who want to create architectural designs that strive for aesthetics. This, however, increases the value of the modules, as the cost per Wp is higher due to lower efficiency compared to the traditional Blue.